RADON GAS IS A MAJOR CONCERN IN CANADA
We are Certified Installers under the CUFCA RADON RSC SYSTEM
Changes to the National Building Code in Canada are focusing on new energy requirements that are making it mandatory to insulate below a concrete slab. The minimum insulation value must be R-5 or R-12 over the entire surface. In addition, protection against underground gases (subsection 9.13.4 of the NRC) mainly radon gas, must be installed to comply with this requirements. Ecologic Radon Barrier System takes advantage of use of 2lb close-cell spray foam that not only provides insulation but forms a perfect seal in a single application keeping occupants warm inside and radon gas, outside.
With an R-value of R-6/inch applied 1 ½ (38mm) thickness, Ecologic Foam provides an insulation of R-9 beneath the entire surface of the concrete slab, exceeding the code requirements. The product is sprayed directly onto the crushed drainage stone providing continuous seamless layer of insulation, free of joints. Ecologic uses Grizzly Gold CCMC 14133L approved 2lb foam that has a high resistance to compression (28 psi). Workers can walk over the foam with equipment without damaging it; the product does not crack or break apart. In a single step, the spray foam can usually be installed in a single day and requires only one application.
The Canadian government has modified the threshold for underground gases. The new requirements of the Canadian Building Code necessitate the installation of an air barrier system under the slab to prevent radon gas infiltration. The unique physical properties of close-cell foam allow it to perform with a high insulation factor but equally perform as an excellent air barrier and vapor barrier. 1” (25mm) of the foam will exceeds 500 times the air barrier material requirements and provide an air barrier system. When applied, the foam expands 30 times its volume in 5 seconds sealing the entire surface. All columns, plumbing vents, sum, drains penetrating the sub and walls are sealed during the same application. Unlike other products on the market, close-cell foam insures seamless impervious work, with exceptional sealing properties, preventing underground gas infiltrations. 2lb close-cell spray foam applied under the foundation walls and rim joists, provides a completely sealed and continuous shell from slab to ground level floor. Likewise, a thermal break between the foundation and the slab is required (minimum R-4 to R-10). The seamless continuity of the spray polyurethane between the concrete slab and the wall ensures thermal break.
The radon barrier system also can be used on floating engineered basement floors which are positioned above the ground creating a crawl space underneath. In this case, spray foam thickness is increased to a minimum of 2 1/2” to create a tub encasement of the crawl space. The foam is sprayed directly on the ground, continued up the pony wall and over the rim joist pockets of the subfloor to seal. No additional slab concrete is required on top of the foam as long as adequate drainage and sump pump system is correctly sized and installed. This is also an ideal solution for crawl spaces created under additions added to existing homes to seal the open earth floors that are common place in Manitoba.
With the R-6 per inch of spray foam is easy to reach the foundation code requirements creating a thinner wall and saving floor space. Another advantage to insulating the basement in one step (i.e. insulating under the slab, foundation walls and the rim joists) is saving in both time and expense. In one single step, we achieve a perfect seal of the building envelope. Close-cell foam provides insulation, air barrier and vapor barrier of a superior quality in one efficient application. According to a CMHC study, the adhesion and quality of the spray foam insulation remains intact in the long term. The adhesion to concrete walls is perfect; there is no possible room for condensation to accumulate and for mold to develop. At 3” (76mm) thickness, close-cell spray foam stops the cold transfer through exterior concrete foundations, thermally relaxing the basement and thereby reducing the effects of stack pressure which contributes to heat loss.
The Ecologic Radon Barrier System is a superior solution!
What is radon gas?
Radon gas is a naturally occurring gas in the ground that is colourless, odorless and radioactive. It comes from uranium as it breaks down in the soil and rocks.
Why should we be concerned about it?
Radon gas is the next leading cause of lung cancer behind smoking. Radon gas easily moves through the soil and enters the air we breathe. When radon gas enters homes and buildings, it can reach levels that may pose a risk to health, where long term exposure to high levels may increase the risk of developing lung cancer. Radon gas is measured in Becquerel’s per cubic meter (Bq/m3), which is a measure of radioactivity. Health Canada recommends that the average level of radon in the air in a normal living area should not be greater than 200 Bq/m3. The guideline of 200 Bq/m3 or less is meant for areas of the home where someone spends more than four hours per day on an ongoing basis.
Manitoba has historically experienced higher radon values in building than the national average. Health Canada has estimated that about 7 per cent of Canadians and 19 percent of Manitobans are living in homes above the radon guidelines of 200 Bq/m3. (Source: Cross-Canada Survey of Radon Concentrations in Homes: Final Report. March 2012).
What is the best method to address radon gas?
Firstly, prevent it from leaking into the building using the Ecologic Radon Gas Barrier System. Secondly, where high levels exist, or where the basement floor is already installed a negative flow exhaust system can be installed below the slab to remove safely any built up accumulation occurring under the foundation. Install specially designed traps in floors drains will also prevent radon from entering the building. Increase mechanical ventilation via a heat recovery ventilator (HRV) to increase the volume of fresh air exchanges.
An Ecologic "spray foam radon gas barrier" can be installed prior to the concrete basement floor being poured. This adds the secondary benefit of providing a thermal break to the floor slab.

Typical open earth crawl space in a Winnipeg home. Foam is applied continuesly from the common wall, across the dirt floor and up the exterior wall of the crawl space.

This is a raised or "floating" basement floor where the earth floor below was sprayed and sealed continuesly up into the floor joist pockets creating a seamless tub under the basement floor. No more ground moisture or radon gas penetration into the home.
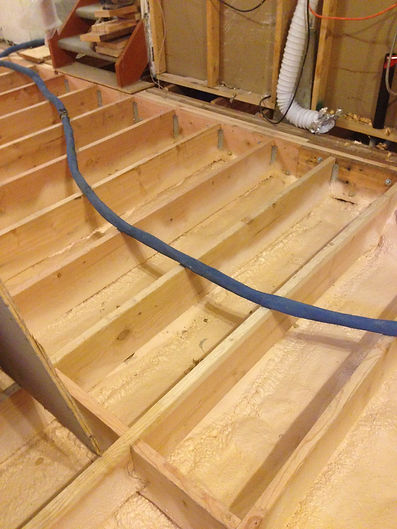
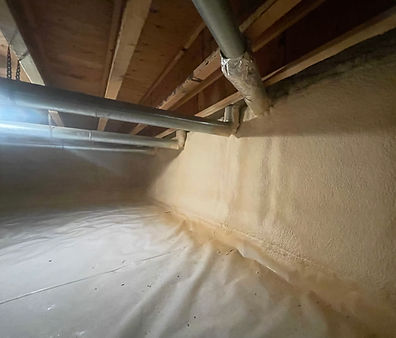